玻纖布生產品質控管
應用主題
根據製程參數暨良率之歷史數據,數據實體系統(DPS)技術可針對製程以大數據模型進行模擬,並據以開發生產良率預測及良率優化應用,提供製程即時預警及最佳製程參數建議。
應用內容
藉由智能裝置即時收集與監控之工業數據基礎,搭配以大數據分析及人工智慧演算法建模之技術,協助製造企業進立關鍵製造工藝之即時良率監控及良率預測模型,以期提前掌控品質偏差徵兆及風險,並採取必要之品質不良矯正措施,提升整體製造產出之品質。
應用技術
本項目系以數據實體系統(Data-Physical Systems,DPS),透過大數據及機器學習技術從企業資訊系統及工業物聯網裝置所累 積的大量工業大數據中,自動學習及解構出能代表真實世界每個物件或作業在虛擬世界的「數據雙胞胎(Data Twin)」。以「良率控制及預測作業」為例,DPS透過ERP、MES和物聯網系統收集製造過程的生產參數、設備聯網資訊及品質檢測等數據,在數據世界創造一個虛擬的「良率控制作業」,協助製造工廠進行良率控制作業,並在異常狀況發生前,提早通知並給予智能處理建議,提升整體製造的工作效率,進而為企業創造更大的營運效益。
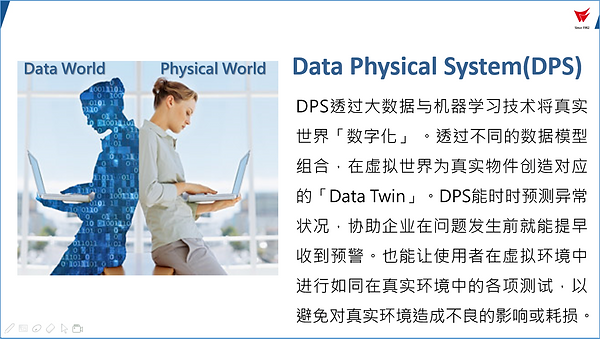
應用案例
案例背景
案例公司成立於1958年,從事 PVC 管、膠皮、膠布等塑膠二次加工的生產。因應六十年來市場環境的變遷,目前產品主要聚焦在塑膠加工、石化、聚酯及電子材料等四大類。
其中,案例工廠主要生產電子級玻纖布,其具有高開纖、低中空、耐高濕絕緣性(anti-CAF)等優良特性,可廣泛應用於IC載板、HDI、MLB材料,適用於各領域印刷電路板(PWB),如:IC封裝、汽車板、通訊板、手機、NB、家電。
面臨問題
玻纖布的生產品質控管,主要透過品管人員檢測玻纖布裏面的大小毛羽數量多寡來決定,當大毛羽數量大於100或小毛羽數量大於2,000,即表示生產品質有問題,過往透過品管抽檢及運用田口品質統計分析來找出品質問題,再進一步探討工藝哪里出現了問題,並加以改善。
解決問題與挑戰
透 過物聯網累積了大量數據後,試圖用大數據建模來分析良率問題,透過更自動化與全面性的方式來找出影響大小毛羽數量的前三大關鍵因數? 這些問題發生在哪些工藝站? 最終工藝參數該如何調整? 是否可以建立良率預警模式而提前預防?
案例專案解決方案
透過搜集多部工藝機台與檢測機台所累積的大數據,經由專案團隊與客戶團隊討論「工藝參數篩選流程」,包括定義問題、搜集與處理資料,數據理解到工藝參數篩選,最後找出影響工藝品質的關鍵因數。過程中,經由大數據建模進行工藝參數關鍵因數分析、工藝關鍵因數關聯分析、工藝參數最佳化模擬,最後建立工藝優化數據實體系統 (Data-Physical Systems,簡稱DPS模擬器)[注1],做為生產過程的可視化模擬。

以本案例專案「良率控制作業」模擬為例,DPS透過ERP、MES和物聯網系統收集製造過程的生產參數、設備聯網資訊及品質檢測等數據,在數據世界創造一個虛擬的「良率控制作業」,該作業功能包括良率即時預警及工藝優化模擬。
良率即時預警:即時分析每一個機台的大小毛羽缺陷數量。當對某一機台提出預警,例如漿紗機台002(下圖),可再進一步分析出影響該機臺的問題在漿紗溫度(下下圖)。

工藝優化模擬:透過可控變數的參數設定,例如設定烘箱溫度區間,來模擬最佳可能良率。
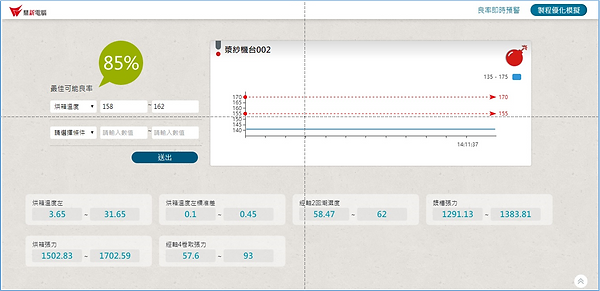
附註:
DPS模擬器:仿照CPS (Cyber-Physical Systems,網路實體系統)建立數位雙胞胎(Digital Twin)的概念,但僅針對企業內部資訊化資料,諸如ERP、MES、CRM、…等各項資訊系統累累積大量歷史數據,進行數據雙胞胎(Data Twin)的建置。換言之,DPS透過大數據及機器學習,從大數據中,自動學習並解構出能代表真實世界每個物件或作業在虛擬世界的數據雙胞胎。
